3D scanners on the construction site
3D scanners on the construction site
are a key step towards digitization that saves both time and money. 3D scanning technology allows the current status of the building shell to be captured digitally. Deviations between BIM planning and the as-built drawings can then be detected and corrected at an early stage. A good example is RoboDog from Boston Dynamics, which is equipped with Faro laser scanners.
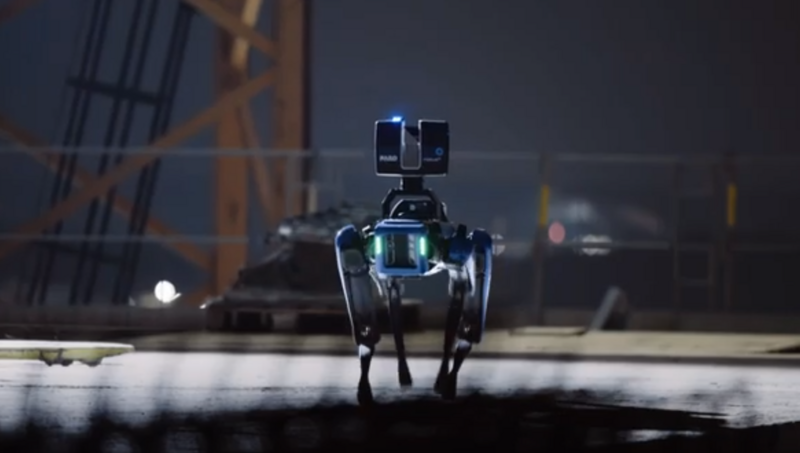
We Have 3D Vision
The human eye perceives up to 16 images per second – not bad. Even so, errors on the construction site often escape the unaided eye, or take a lot of effort to find.
As an innovation leader, Drees & Sommer is involved in optimizing construction processes through the use of digital tools. We begin by examining conventional processes and look for digital approaches that create added value for our clients and our staff members.
The use of 3D scanners is a step towards successful digital transformation. It saves time and costs on construction sites. 3D scanning technology enables the current state of the building’s shell to be captured digitally and matched with the target state specified by the digital plan. In this way, deviations between plan and reality can be discovered early and resolved. This not only saves time and money, but helps to reduce the waste of resources, making the construction process more sustainable.
3D scanners are already being used in construction management, particularly for quality control and construction site documentation. They are in use for some projects at Drees & Sommer. Our experts are also involved in the further development of the technologies with individual suppliers such as Faro Technologies. The aim is to use 3D scanning in future construction projects for maximum added value as part of the digital processes.
To match scanned data with the digital plan, Drees & Sommer uses software from Imerso. With Imerso, the scan results are immediately updated in the digital model, and the target state is automatically compared with the existing state. This startup company, based in the Norwegian capital Oslo, wants to establish 3D monitoring as a new industrial standard for BIM projects. Drees & Sommer is working closely with the young enterprise and is convinced about the benefits of the software.
Digital mapping of established buildings
A NavVis wearable 3D laser scanner is used for this purpose.
Digital Mapping is a highly versatile technology. On the one hand, the model generated can be used during the ongoing operation of a property.Information is stored in the cloud-based model and can be viewed digitally from anywhere. The data available includes both information for customers – such as opening times and contact information – and internal information for the operator, including maintenance logs, technical data sheetsand facility management audit and inspection documents.
Another key application for digital mapping is the generation of floor plans. This is useful where documentation for older properties is out of date and does not reflect construction work undertaken in the meantime. In such cases, our experts can generate up-to-date floor plans and planning documents that reflect the building’s current status.
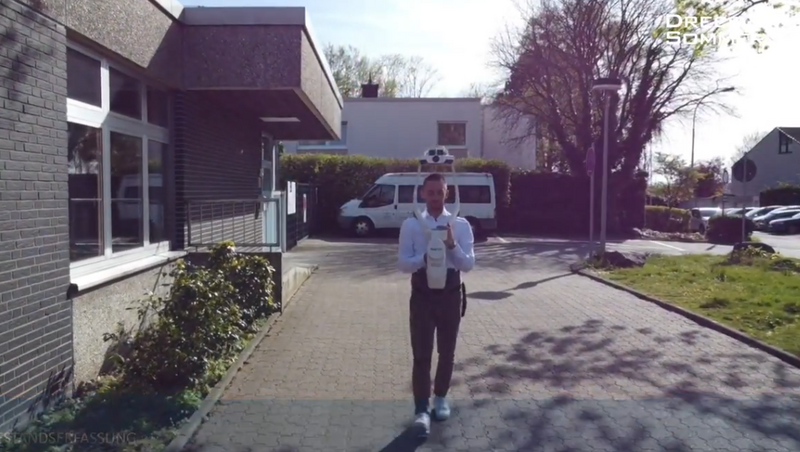
Our aim
Drees & Sommer is committed to the technologies of the future. We investigate the use of different scanning products, identify new needs and tailor our services to meet them.
In other words, we offer a package of services related to new technologies and digital tools and processes – for the benefit of our clients. We believe in working with other companies rather than in isolation, integrating startup technologies to ensure successful innovations.
WE USE THE FOLLOWING 3D SCANNERS ON OUR CONSTRUCTION SITES
NavVis VLX
NavVis VLX is a portable mobile mapping system that allows experts to take high-quality scans of complex buildings and construction sites.
How it works:
The wearer of this ‘backpack scanner’ walks through the shell of the building that is to be captured. The scanner software processes and visualizes the data and maps the interior of the entire building in the browser. This enables measurements to be taken or the plans to be exported to the BIM software to plan change processes.
Application at Drees & Sommer:
Drees & Sommer experts currently have three products in use. These were successfully used in the construction of the new OWP 12 corporate building and further client projects.
3D scanning technology digitally captures the current status of the building shell. This is then compared with the target state specified by the BIM planning. Deviations between planning and reality can thus be detected and corrected at an early stage. This not only saves time and money, but also reduces any waste of resources, leading to greater sustainability in construction.
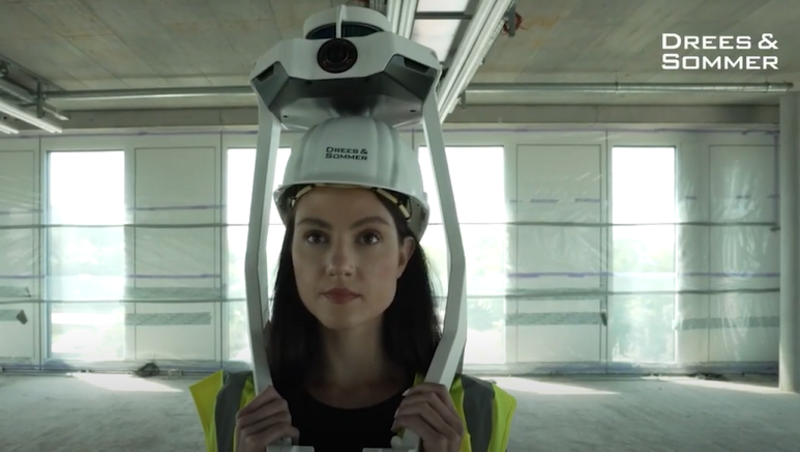
Faro-Trek laser scanner
The Faro-Trek scanner from Faro Constructions generates precise and comprehensive 3D images of construction sites or buildings within a few minutes.
How it works:
The laser scanner can be combined with Boston Dynamics’ quadruped robot (RoboDog), offering the potential for future autonomous use on construction sites. With the scanner on its back, the robot follows predefined paths through the shell construction of the building and scans the conditions at specified points.
Application at Drees & Sommer:
We are working with Faro Technologies on application scenarios for the quadruped robot in 3D monitoring. The robot has already been used for some projects and we look forward to continuing to work toward a digital future with Faro Technologies.
Let's talk.
We look forward to hearing from you!