One thing you can be sure of: Dedicated
Drees & Sommer colleagueswith appropriate professional backgrounds and
competencieswill provide you with products and
servicesthat are tailored to your
sector'sneeds.
Competencies
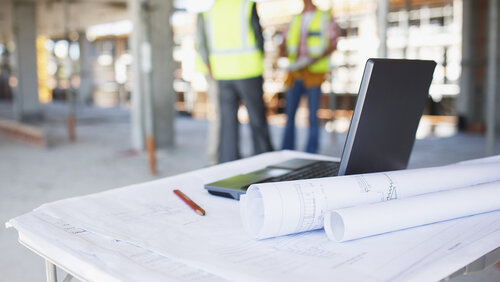
As architects, an integrated planning approach is the focus of our activities. From the outset, our designs incorporate all of the principal’s requirements and the resulting specifications for the individual trades. We use this perspective for the overall functional and spatial coordination of our projects. The modular planning approach is the key method for ensuring overall integral quality. We evaluate the quality of a design based on esthetics and the fulfillment of user requirements. Thanks to our expertise in digital planning (BIM), our experienced colleagues ensure high quality of planning – including detailed planning.
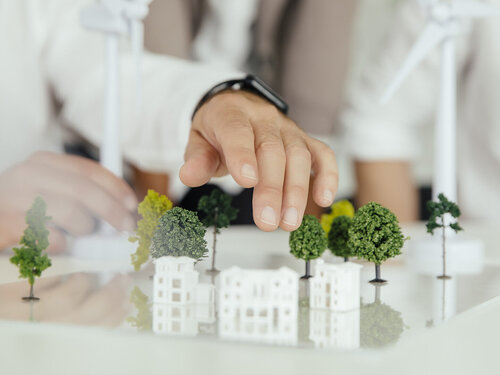
As building physics experts we ensure that statutory sound and thermal insulation requirements are met. We also lay the planning foundations for climate-friendly construction and a high level of user amenity. We work across a range of planning disciplines and help ensure correct realization of planning by contractors on the construction site.
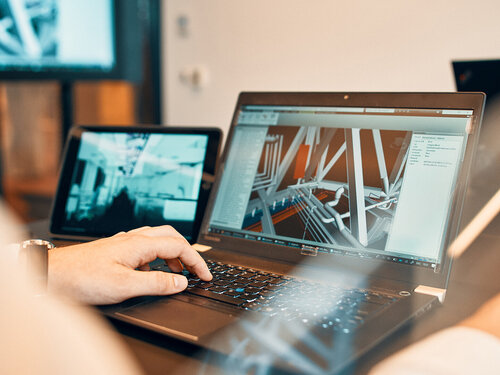
Planning projects generate huge volumes of data that have to be brought together at a central point to coordinate contractors and discipline model. Geometric data, data on technical properties, production process timelines, and cost data. Our role is to prepare multidimensional data from major projects for the principal, project management, designers, and most importantly, for overall coordination. BIM coordination feeds this data into the project stages via defined processes.
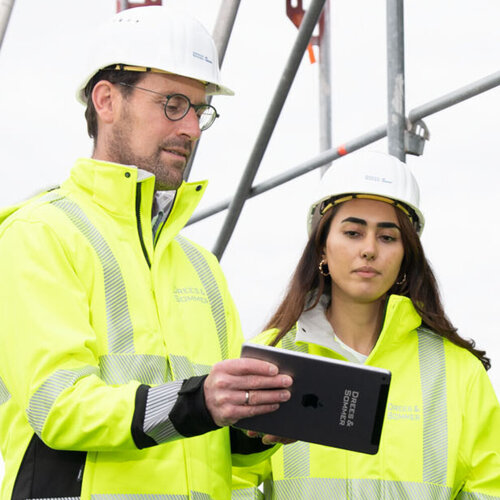
With our Construction Management (CM), we provide project management and integral construction management from a single source. We control the planning, awarding and execution of the project according to the client's specifications, taking particular account of the factors of cost, time, quality and good cooperation. The special feature of Construction Management is an all-embracing consulting approach. This approach also includes the expertise of the executing team. With our Lean Management, we coordinate planning and construction processes in the best possible way to optimize building production.
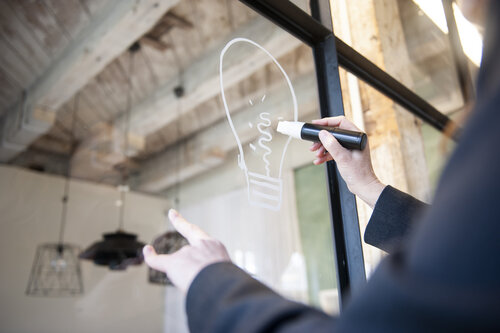
Whether for a new or established building or for building systems equipment – our consulting services cover all your energy issues. We act as the interface between the various architectural planning disciplines, including user analysis, facade, building physics and building services engineering. Our Energy Design team develops sustainable energy concepts that are cost-efficient and have low carbon emissions. Our simulation tools allow rooms, facades and plant & equipment to be analyzed and precisely adapted. We undertake energy and decarbonization audits to identify measures to make your building EU Taxonomy-compliant.
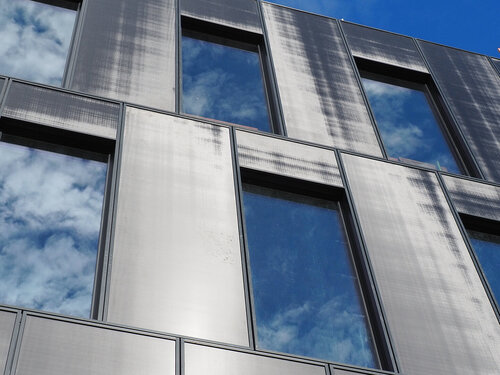
Facade engineering involves the development of facade concepts in close partnership with the principal and architect. Our role is to make the architect’s design more cost-efficient, to ensure the functionality of the facade, and provide cost certainty from the outset. Our engineering is product- and system-neutral – which means that we are in a position to provide competent advice to our customer at any stage of planning.
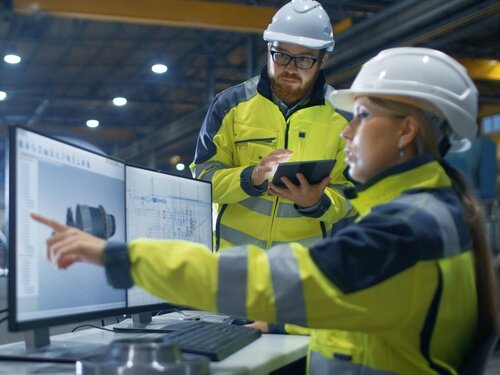
Our General Construction Management (GCM) team takes over complete responsibility for the execution of your project. We combine project management, planning services and construction management into a complete package, thus ensuring smooth planning and execution processes. In combination with our BIM management service, GCM allows extremely economical planning and execution processes to be realized in a short time.
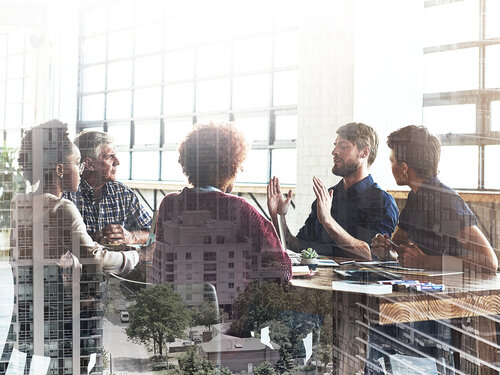
In major planning projects, we take on the role of overall coordinator with the goal of fully coordinating the physical and functional interfaces between contractors. Depending on the size of the project, this role may be the responsibility of a single designer or a whole team. We use agile methods and digital tools for coordination and communication, and to track planning progress. Efficient overall coordination plays a key role in ensuring the cost-efficient and successful completion of projects.
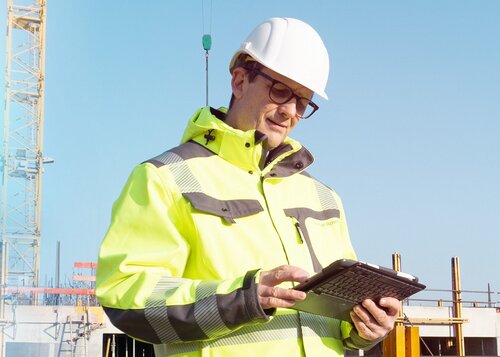
Ideally, specialist planning competency in building construction disciplines and building services engineering (BSE) must come together to ensure that a building site operates smoothly and that the construction project remains cost-efficient. Integral Construction Management achieves this. Using Lean methodology, we consolidate all construction management services for cost groups 300 (construction works), 400 (BSE) and 500 (external works) into a single service for the entire construction phase – from invitation to tender through to building operation.
In service phase 8, generally known as site management, we manage execution planning for cost groups 300 to 500. We create a schedule, document construction progress, and take responsibility for site supervision. We also coordinate cooperation between the contractors involved, inspect and approve building work, and take responsibility for auditing of accounts and cost control. In this way, we ensure the cost-efficient completion of work on schedule and in top quality.
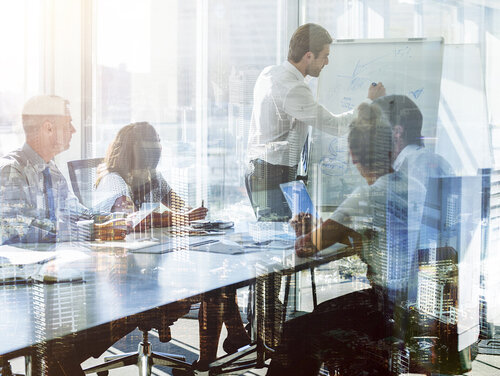
By acting as a professional ‘temporary project department’, Drees & Sommer supports you by undertaking all delegable tasks for the duration of the project. A project organization that is tailored to your requirements and our tried and tested schedule and cost control services combined with quality surveillance ensure cost-efficiency and adherence to the binding overall budget and quality standards within agreed realistic timeframes.
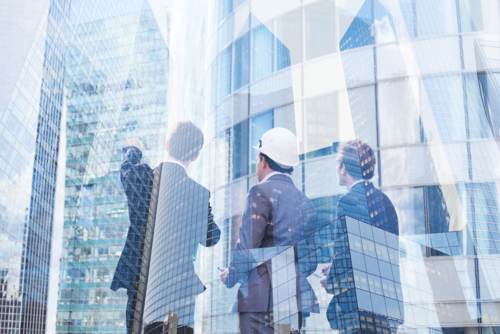
Whether purchasing or selling properties, accurate and reliable information is the basis for a successful transaction. Our Technical Due Diligence service provides you with concrete data on the key data and quality of properties, as well as their value enhancement potential, risks and possible deal-breakers. A detailed on-site inspection provides a sound basis for decision-making.
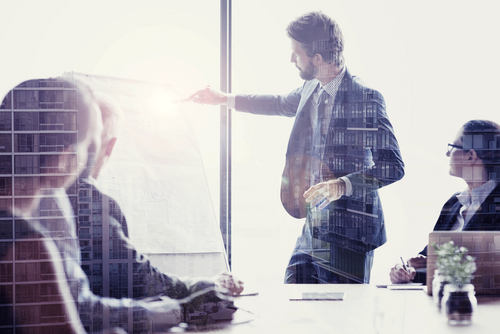
Our project team advises the client and supports planners by providing technical & economic construction consulting. We check planning content for compliance with the functional, qualitative and economic requirements of the project and, if necessary, arrange for revision of the plans, thus ensuring that everything continues to work smoothly after handover.
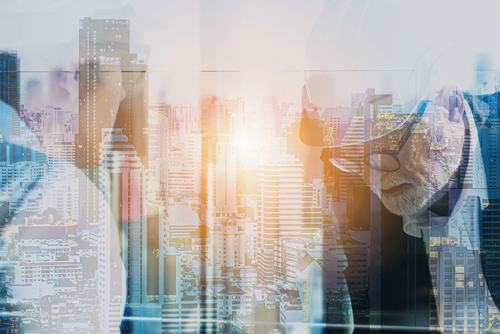
Our building services engineering (BSE) service develops and plans energy-saving, economical concepts for your building. Our teams of experienced BSE experts are accustomed to working across all disciplines. Collaborating with you, the principal, and the architect, we develop and realize sustainable technical solutions that work from the outset.
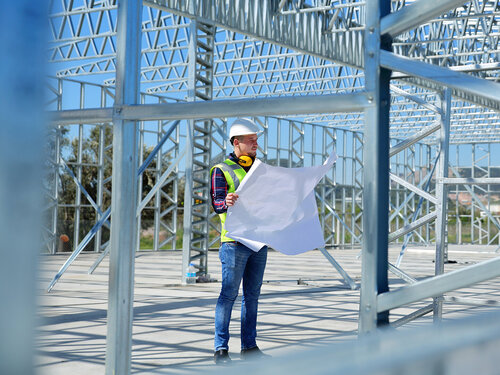
Whether high-rise buildings, airports, railway stations, or bridges – structural engineering is the basis for the design of every building. Structural engineers at Drees & Sommer realize innovative projects – designed to be appropriate for the materials used. Our focus is on developing load-bearing structures using state-of-the-art digital tools and planning processes. We provide our customers with competent, objective advice, while always taking the ecological impact of our work into account.
- Architecture
- Construction Logistics
- Building Physics/Acoustics
- BIM Coordination
- Construction Management
- Energy Design
- Energy Infrastructure and Energy Sector
- Energy Management
- Facility Management Consulting
- Facade Engineering
- General Construction Management (GCM)
- Integrated Coordination
- Integral Construction Management
- Modular Planning
- Site Supervision
- Project Management
- Real Estate Consulting
- Technical Due Diligence
- Technical and Economic Construction Consulting
- Building Services Engineering
- Structural Engineering